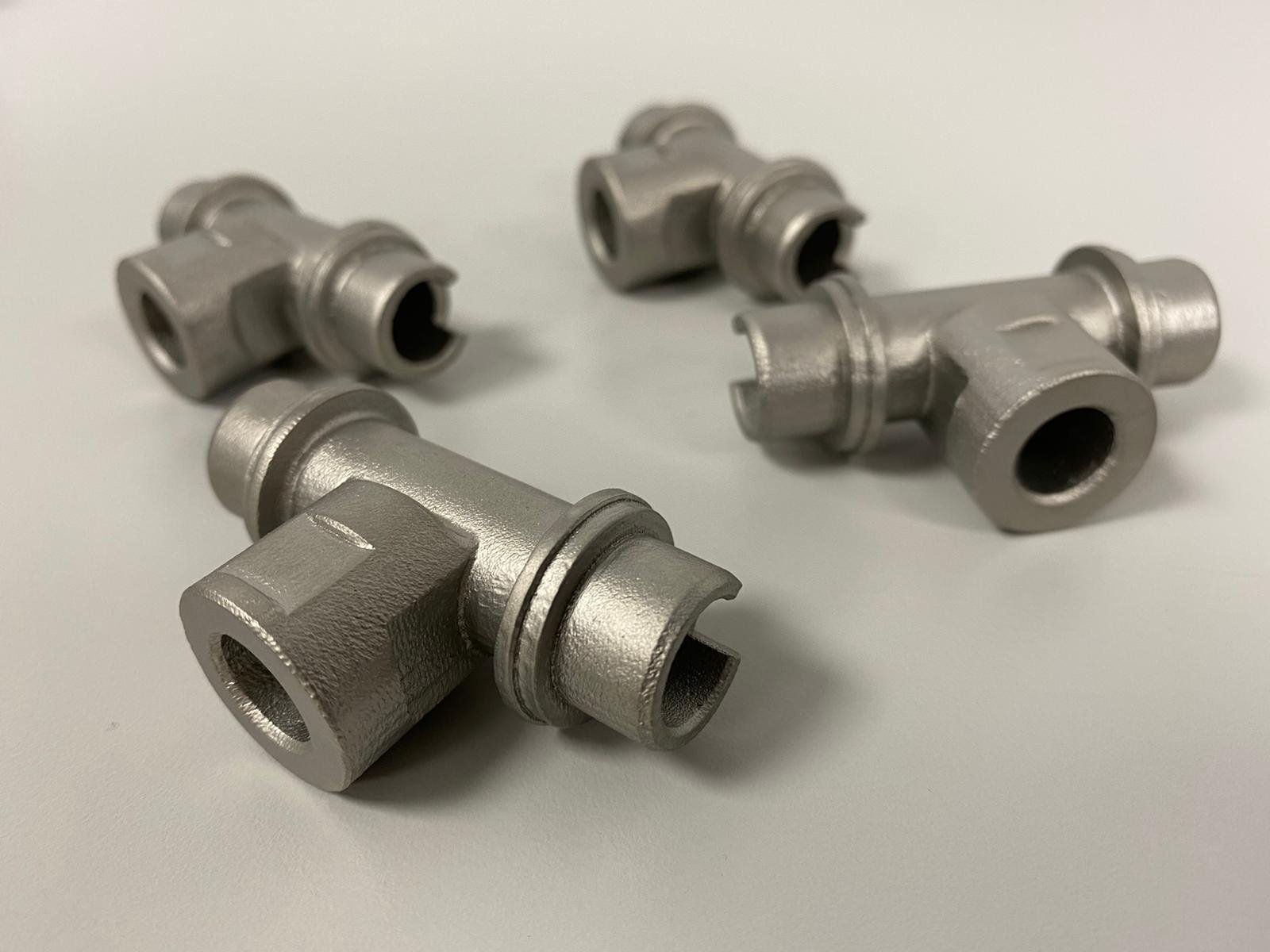
Bespoke Racing Bike Components
Last year, OMG Racing Ltd approached us to collaborate on producing some bespoke components for a custom race bike that the company was in the process of developing.
The parts were custom-designed by our client and prototypes were printed in a photopolymer to verify the design and fit of the part. Once the prototype had been approved and verified, the task was then to get these produced; in metal and TPU respectively.
Options for both stainless steel and titanium were considered for the Fuel Line T piece using the DMLS process (Direct Metal Laser Sintering). This process uses a high power laser to both melt and fuse thousands of layers of metallic powder in order to produce the part. The powder system meant that parts, such as the Fuel Line T Piece could be produced without concern of built up support in the internal channels. The client settled on stainless steel as the most appropriate option and is still currently in use as an end-use part.
For the bellmouth piece, the client required a TPU material. We explored multiple options including both FDM and Polyjet processes in order to achieve the requirements, but ultimately settled on Ultrasint-TPU 90A-01 on the HP Multi Jet Fusion. The MJF process offered a low-cost solution while providing an appropriate shore hardness for the application, and much like the DMLS process, the powder-based system could make easy work for the part.
Additive manufacturing offered a quick turnaround for a client that was under tight timescales to deliver in time for an event that traditional machining methods wouldn't have been able to achieve.
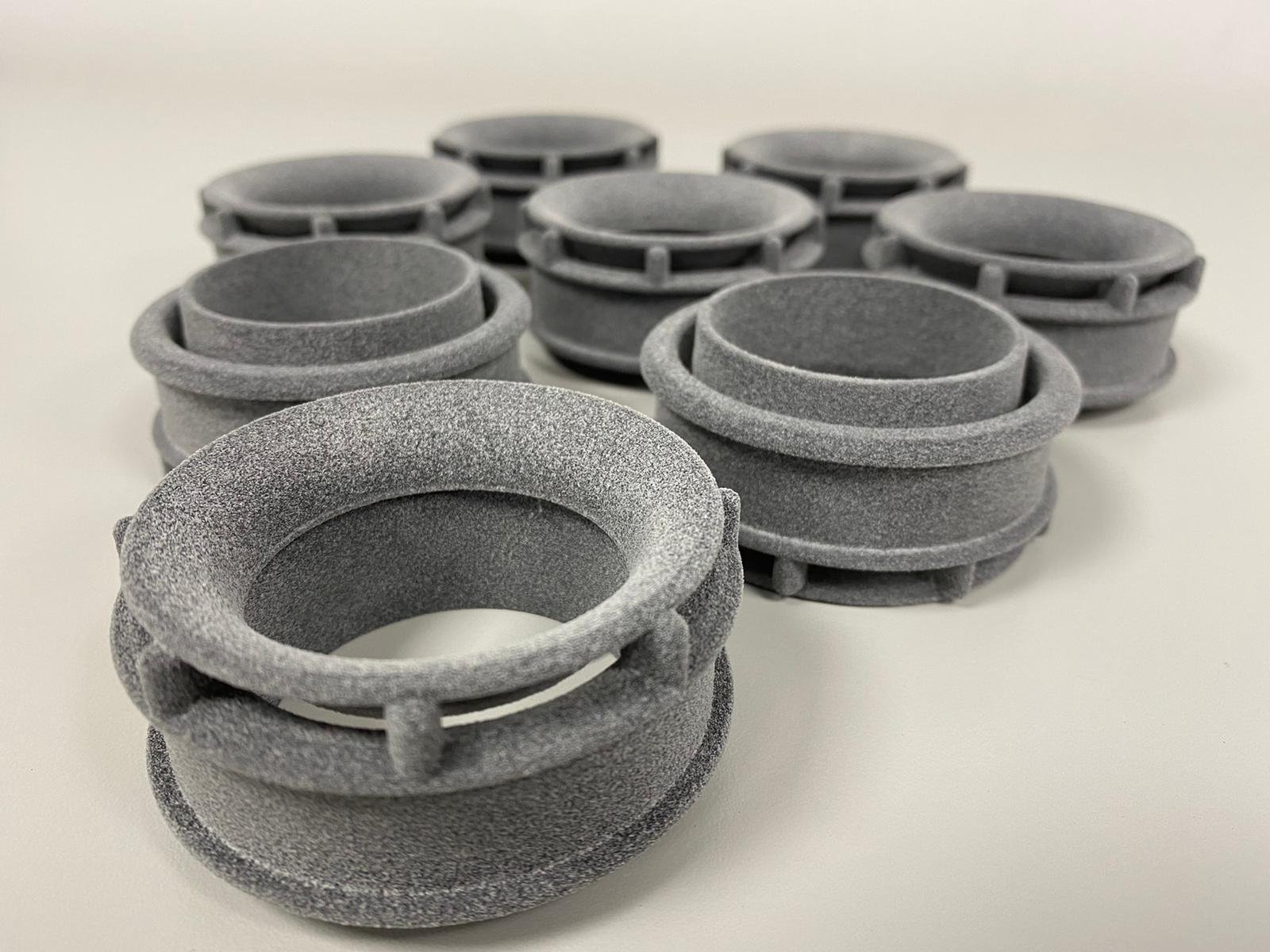
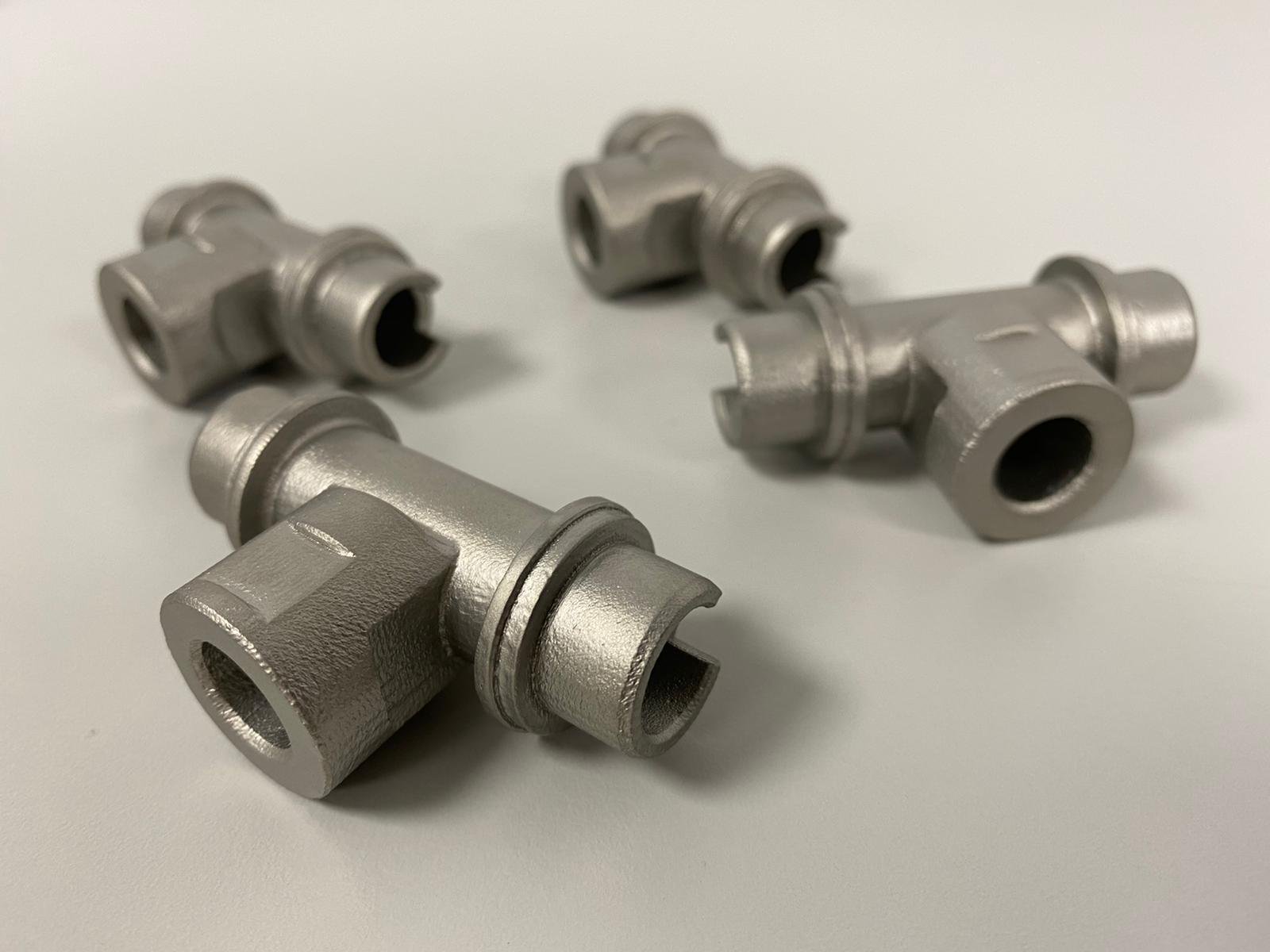
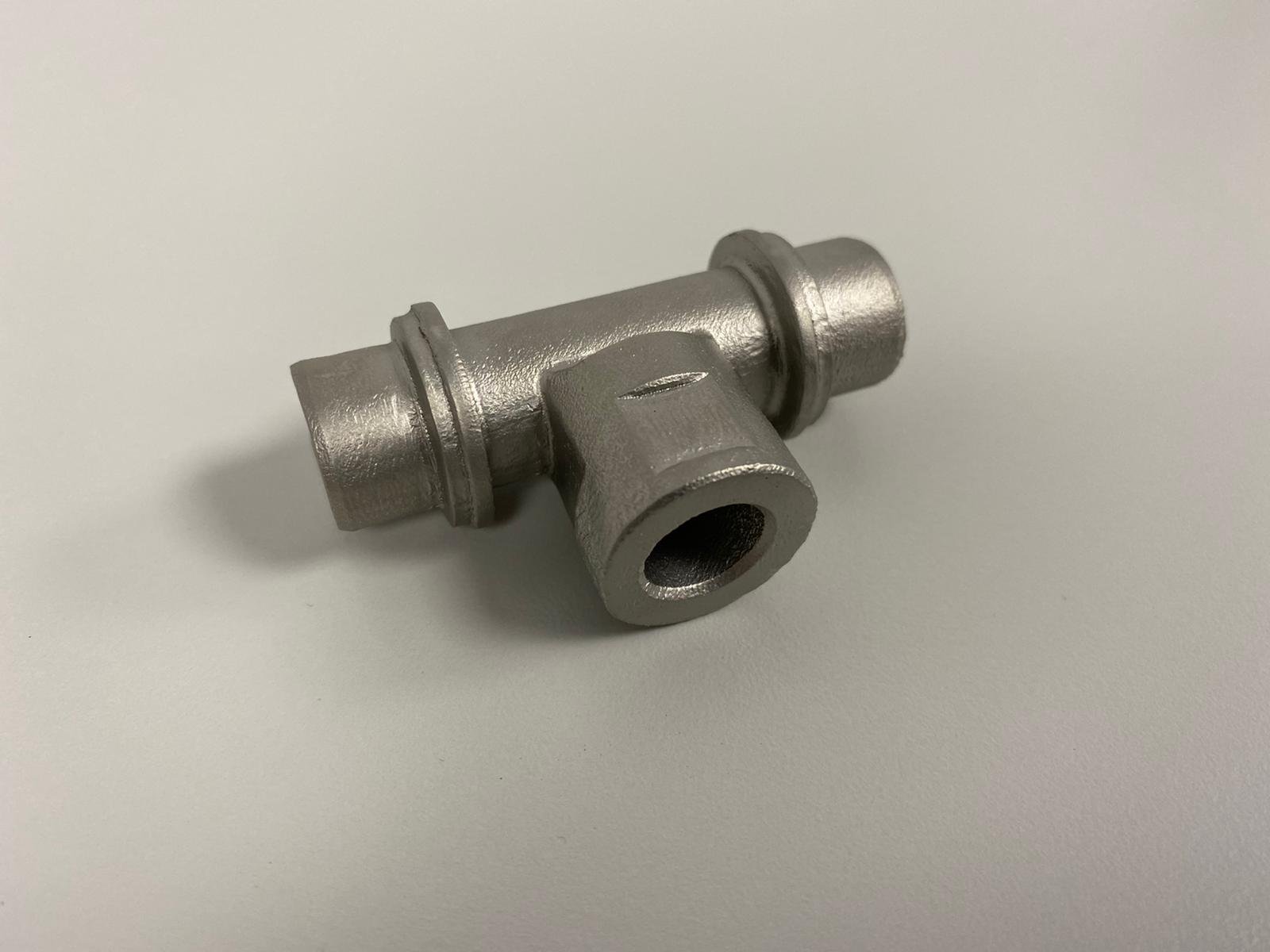